Blasting systems
Twister and Tornado
As the official Swiss contact for sandblasting systems, we sell the Twister and Tornado models from the manufacturer BMF GmbH. We also offer full service and training.
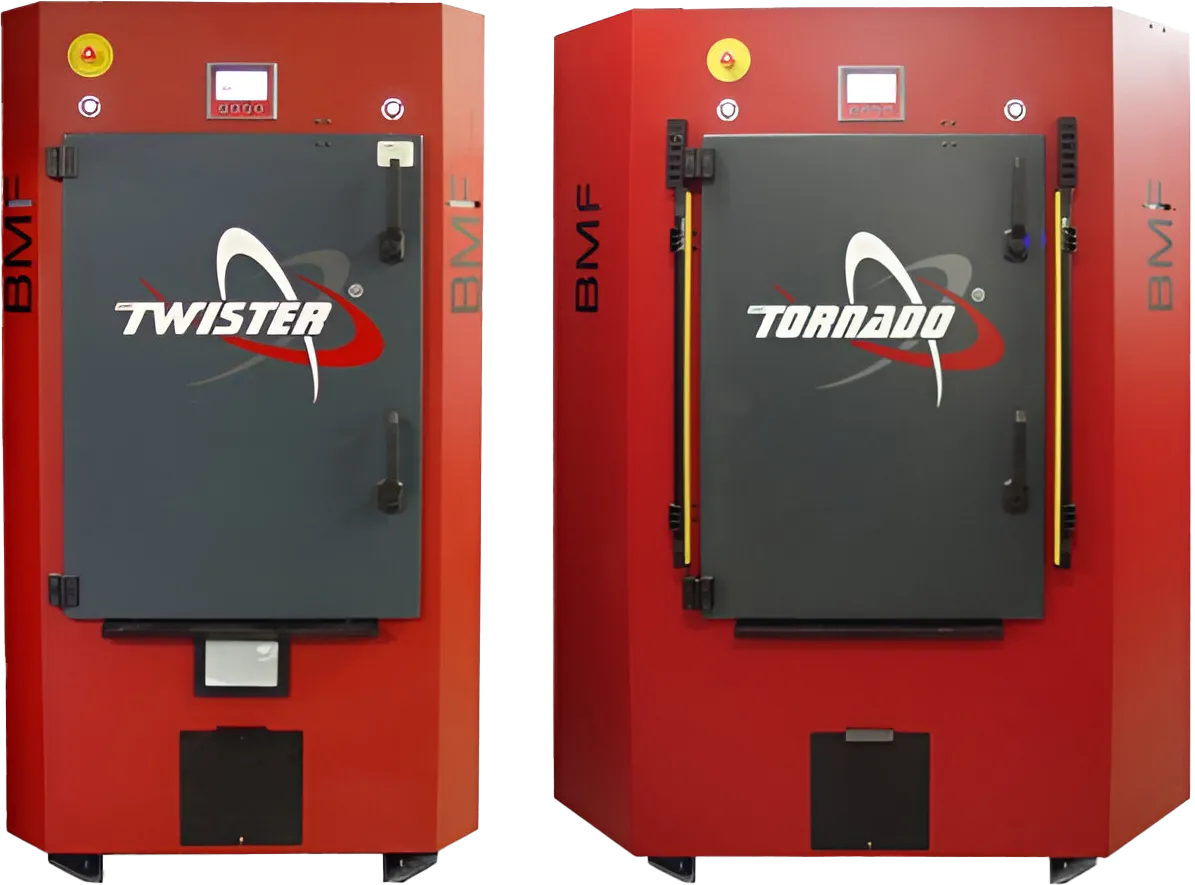
The revolution in blasting technology
Blasting without compressed air
For the first time, the blasting systems allow you to process the blasting material in conjunction with a blast wheel. The newly developed blasting process works without expensive compressed air.
Homogeneous surfaces
The innovative arrangement of the functional elements and their kinematics ensure even blasting of all surfaces. A quick-change system saves time when attaching the parts.
Energy efficiency
The Twister and Tornado systems process up to 100 parts simultaneously, save up to 90% energy and utilise the abrasive longer and more effectively.
Twister and Tornado
With the unique BERNSTEIN TWISTER and TORNADO blasting systems, you can achieve homogeneous and reproducible surface structures with minimal technical and energy expenditure compared to conventional sandblasting cabinets. The central blast wheel with the patented blade geometry throws the abrasive against the parts located on a satellite support. The workpieces are moved on a conical orbit around the rotating blast wheel.
A quick-change workpiece system enables time-saving mounting of the parts to be processed, and the machines are identical in their function. They differ only in their dimensions and the maximum size of the parts to be blasted.
Twister | Tornado | |
---|---|---|
Machine dimensions | 1 x 1 x 2m | 1,5 x 1,5 x 2m |
Workpiece holders | 10 | 10 |
max. part diameter | 140mm | 250mm |
Weight | 600kg | 900kg |
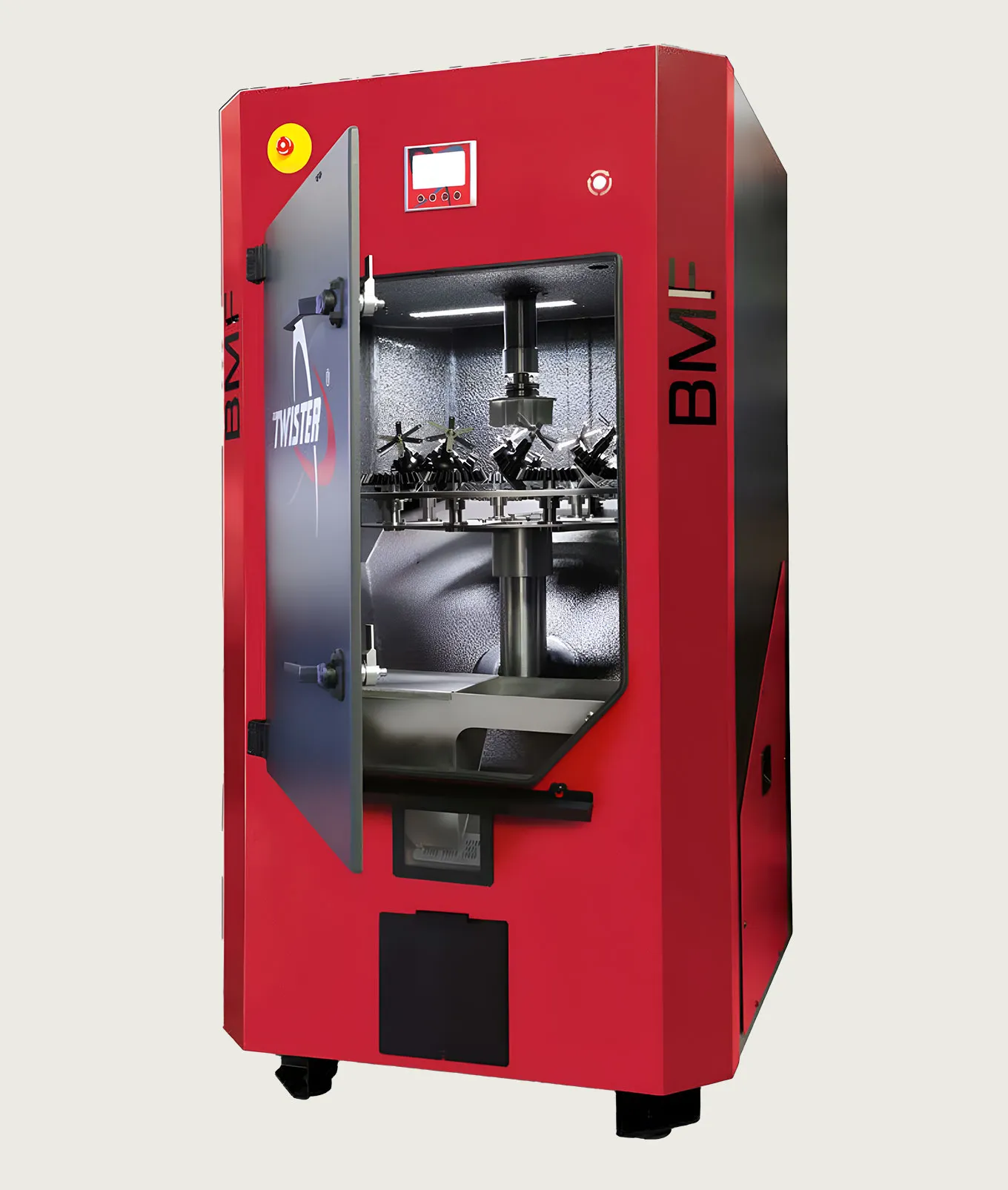
Smart Surface Control
The innovative SMART SURFACE CONTROL technology makes it possible to programme the optical and physical properties of surfaces. This technology also allows the actual construction process to be customised in terms of the desired surface, and BMF's unique systems have been awarded the German Federal Prize for Innovation, the Saxon State Prize for Innovation and the Central German Innovation Prize, among others.
Construction and spare parts from the 3D printer
The workpiece holders and the gear wheels of both machines are manufactured on 3D printers. The base materials have proven to be very wear-resistant even under heavy loads. This means that they can also be used in the blasting area without any concerns. In addition, a weight reduction of up to 60% can be achieved compared to milled parts.
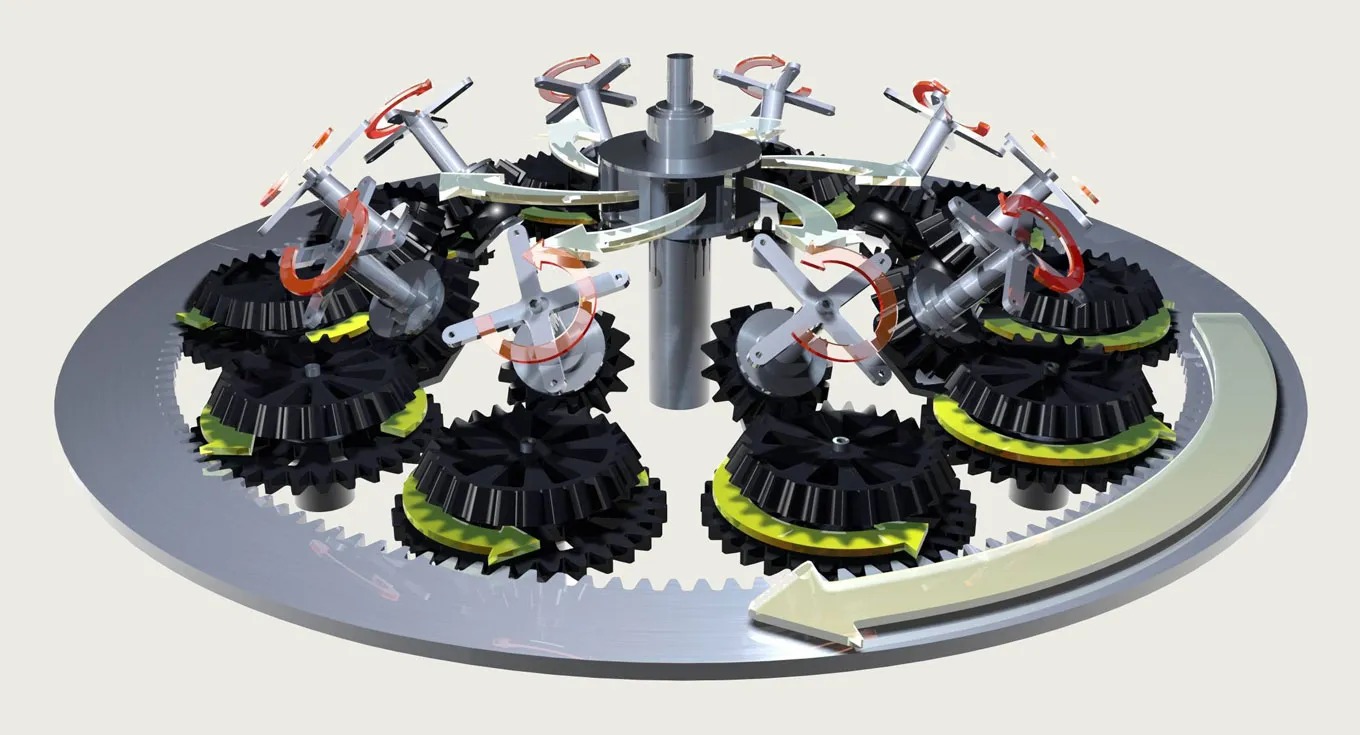
Automation
With the addition of the robot-controlled parts magazine, which is available for Twister and Tornado, you can deploy your employees for other tasks and even have the systems work fully automatically overnight. From now on, our Job Manager takes over the control of the blasting systems and ensures that all components are processed with the required surface quality. 60 - 500 places are available in our parts magazines, depending on the part size and expansion stage.
By effectively utilising the "UR 10" robot, additional processes such as measuring, laser marking or packaging can be effortlessly integrated into the workflow. The productivity of the blasting system can be significantly increased by using the job manager.
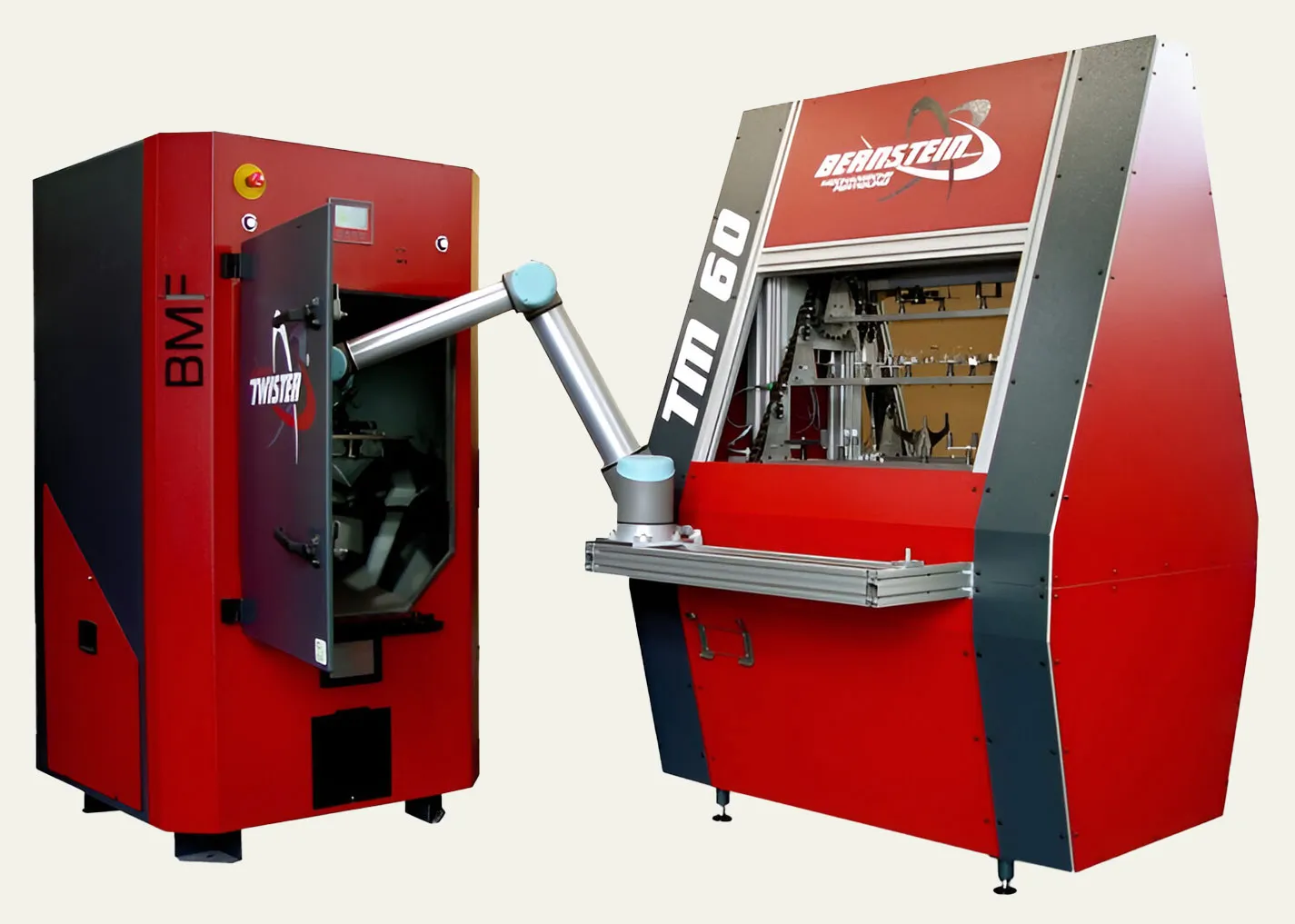
Benefit from the Twister and Tornado
- Machine and device construction
- Additive manufacturing
- Watchmaking industry
- Medical technology
- Surface technology/ surface finishing
- Automotive engineering
- Special machine construction
... and maybe you too.
Downloads
Arrange a consultation
Maximise your productivity with our comprehensive services. Find out how we can improve your production facilities during a personal consultation.
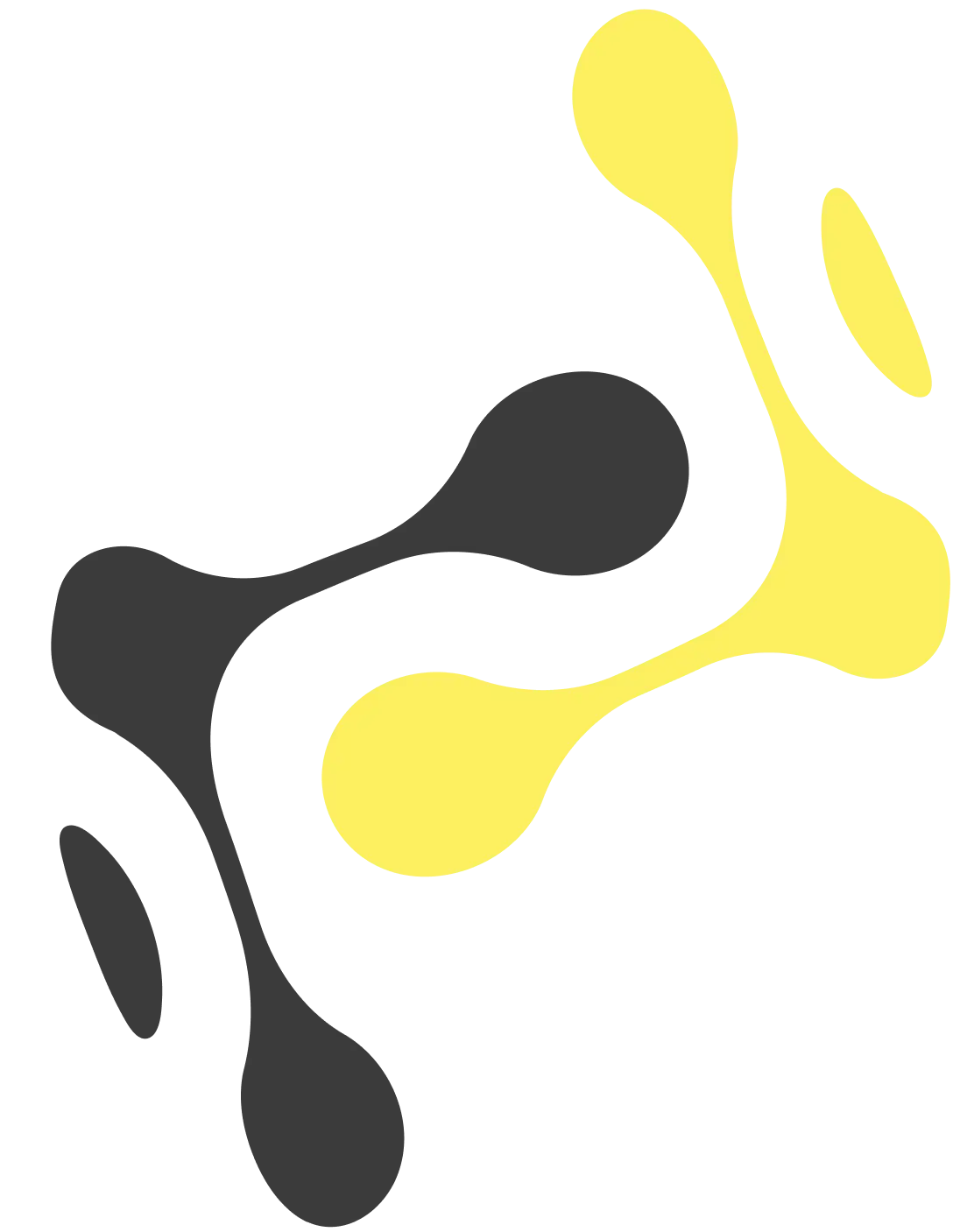